(GMP) Manufacturing
Your process is ready. Toxicology studies are on the way. Now it's time to take your product candidate to the GMP level.
Our manufacturing services ensure fast and reliable GMP-stage production. We do this by leveraging our expert team's experience to convert development protocols into safe, high-quality batches. By offering high-tech bioreactor systems for both in-house and external processes, we help customers achieve efficient and scalable production.
Pre-Clinical and GMP-Compliant Manufacturing for Biologics
Since 2002, clients from all over the world have trusted our good manufacturing practices (GMP) to produce their antibodies and recombinant proteins for clinical use.
We are committed to nothing less than your success. And we achieve this in a competitive time frame. Our expert team's long-standing experience ensures the fast and reliable conversion of all development protocols for the GMP-stage as well as the safe manufacturing of single or multiple batches. We offer our services both in-house and for externally developed processes.
We offer GMP production in fully state-of-the-art disposable systems in fed-batch and continuous processes in up to 1000L bioreactors. We rely on our own chemically-defined media platform, including in-house media and buffer preparation.
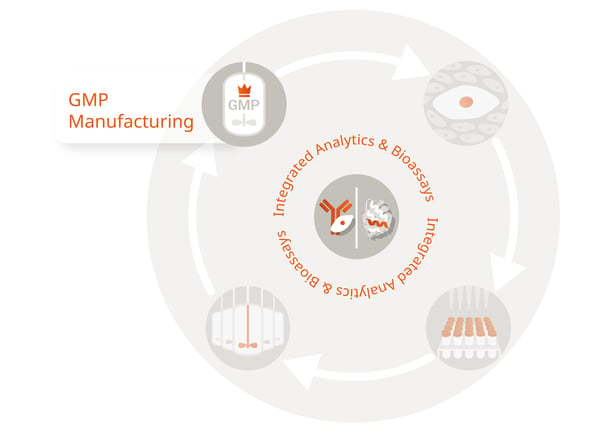
Holistic Approach from Development to Production
Our integrated approach to GMP manufacturing, from cell line development to production, ensures reliable, scalable results. Key quality features are defined early, with close collaboration between development and production teams. A dedicated process manager oversees all CMC activities, keeping the customer involved and informed throughout.
Robust Platform Processes
A platform process is available for monoclonal IgG 1 and IgG 4 antibodies. Cell culture parameters and downstream steps are predefined and only need to be slightly adjusted to the needs of the individual clone and molecule. This accelerates the transition from development to GMP manufacturing. Production titers of ≥ 4g/L and downstream yields of around 80% can be expected. Down-scale models for process transfer and potential investigations during production are created. The platform process also serves as the basis for the process development of new antibody formats, albeit typically with further modifications to ensure high product quality.
Capabilities and Scale
We use fed-batch processes in 250L and 1000L disposable bioreactors, depending on the required amounts of clinical material.
We operate three production lines with a culture volume of up to 1000L. Media liquefaction and buffer preparation takes place on a separate clean room floor and is also covered by our manufacturing license. Containers for media and buffers are then connected through the wall and placed outside the production rooms in the CNC area. Open process steps, such as hose connections, are largely avoided. When necessary, they are carried out in the presence of a portable device that also cleans the ambient air.
State-of-the-Art Facilities and Equipment
All equipment that comes into contact with the product is disposable in order to avoid cross-contamination and allow for quick product changeover. Modern equipment from market-leading providers is used in production. We follow the open-source concept for consumables. Only materials that are publicly accessible are used. Upon request, the customer receives purchasing authorization for commercial providers for our own chemically-defined (CD) cell-culture media platform.
In-house Analytics, QMS, and QP
The whole process is steered by a comprehensive and audited quality management system. An internal Qualified Person (QP) is responsible for releasing the drug substance.
Analysis methods for IPCs and release tests are established and qualified by our experienced teams. Only some biosecurity testing, particularly for MCB and raw material testing, is outsourced to external providers. We have separate QC teams for incoming goods' inspection and stability testing as well as for IPC and final product release testing. The final approval is carried out by our internal QP.
Pre-Clinical Manufacturing & Manufacturing of Clinical Batches
We produce to your needs. We provide you with early material and small-scale production using clone pools or final clone material for extended characterization, pre-clinical testing (batches for tox-studies), or technical runs for manufacturability, process robustness, and comparability.
Our clinical manufacturing refers to the production of material that is used in human clinical trials. We adjust USP and DSP scale to the API amount (active pharmaceutical ingredient) required, resupply opportunities included.
We stand for the Magical Quadrant
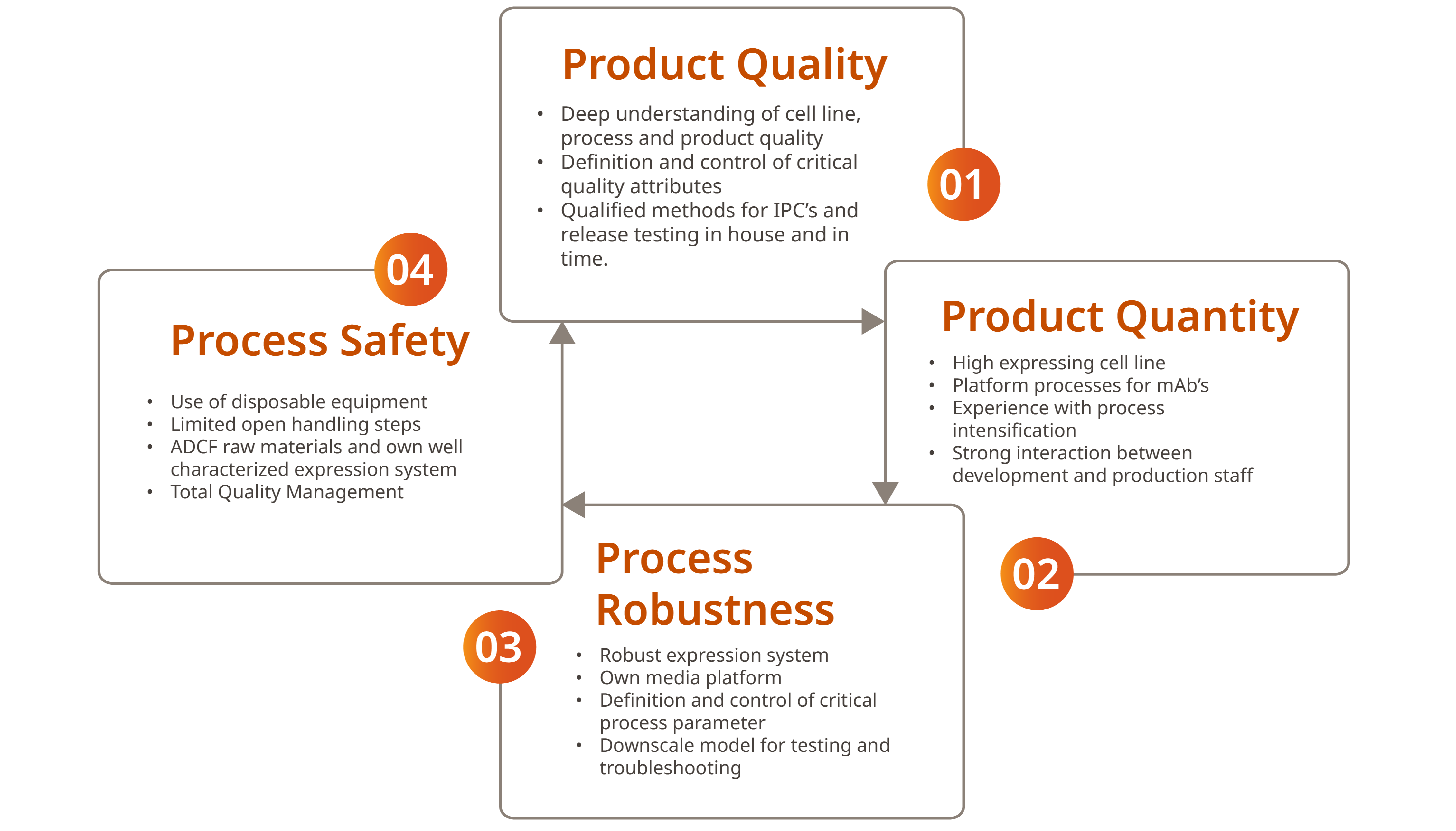
Our Promise To You
Safety First
- Disposable concept
- Raw material free of animal components
- Qualified vendors
- Release methods estabilished and quailified in-house by experienced teams
Effective Processes
-
Integrated approach of development activities up to the first production run
- Platform process available
- Own chemically-defined, in-house media and buffer production
- Dedicated project managers facilitate communication and fast solutions
Compliance / Traceability
- Fast and reliable conversations of all development protocols
- Total quality management system
- GMP certificate